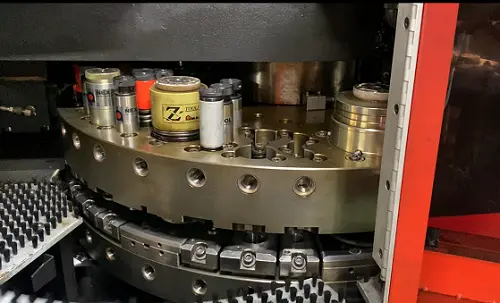
葛飾区で金属加工を営んでいます。
中でもアルミ加工は全体の7割を占め、
アルミ加工の技術力はさまざまなお客様に評価をいただいております。
お気軽にご相談ください。
TEL:03-3692-0444
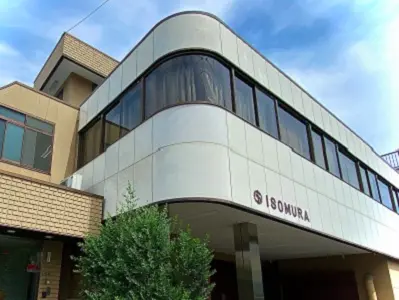
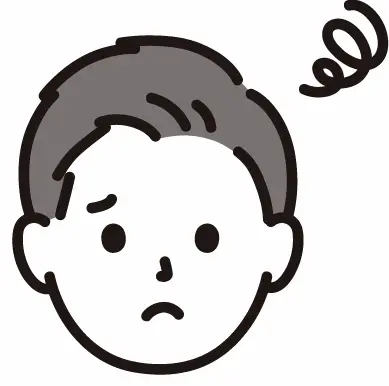
タレットパンチプレス加工ってどんな加工?
他の加工方法とはなにがちがうの?
このような疑問を解決するため、
タレットパンチプレスの
「加工の仕組み」「加工方法」「特徴」
についてわかりやすく解説します。
タレットパンチプレスとは
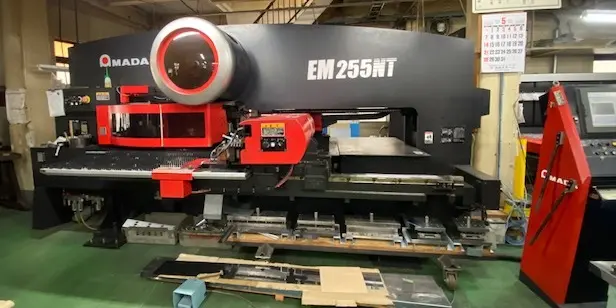
機械の種類としては、プレス機械に分類され、板金加工では主力となる機械です。
通称「タレパン」と略されます。
プレスとの違いは、プレスは製品専用の金型を使用するのに対し、
タレパンは、タレットに数十種類の汎用金型を装着し、プログラムに合わせて自動でタレットを回転させ、加工します。
パンチング加工とは、パンチとダイの間に板材を置き、パンチを上からたたいて任意の形状に穴あけや成形加工をすることです。 NCTは、タレットに数十本の金型を装着し、タレットを回転させることにより必要な金型を呼び出し、材料を位置決めしながら加工を行います。
出典:株式会社アマダ「板金加工の基礎講座 | 第5回 パンチング加工 (Part 1)」https://www.sheetmetal.amada.co.jp/column/course/basis05/
(最終アクセス2023年8月31日)
タレットパンチプレスの加工の様子を動画にしています。
合わせてご覧ください。
加工の仕組み
① 仕組みの基本
丸・角・長丸・長角の数百種類ある汎用金型を組み合わせて加工を行います。
金型には上部金型の「パンチ」と下部金型の「ダイ」があり、セットで使用します。
金型の組み合わせパターンは何種類もありますので、材料がムダにならない効率の良い金型の使用が必須です。
下図は丸金型と長丸金型です。組み合わせ方によって、様々な形状の「穴あけ」や 「打ち抜き」ができるのです。
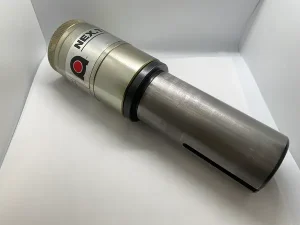

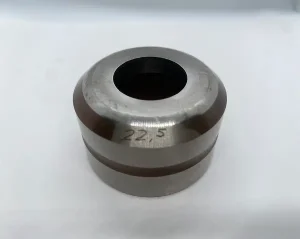
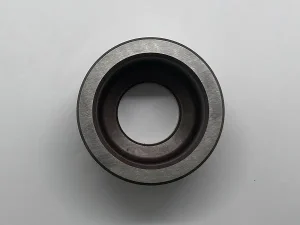
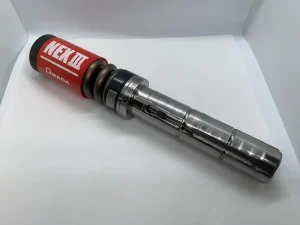
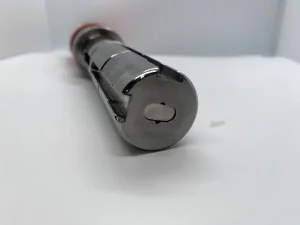
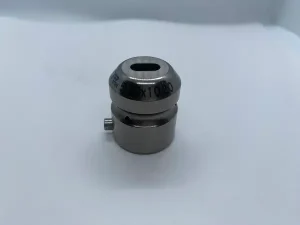
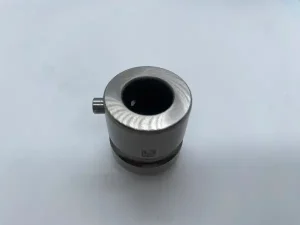
金型は種類によって大きさが異なり、A型(小)~D型(大)まであります。
上図で紹介した金型もA型とB型であり、比較してみると大きさが違います。
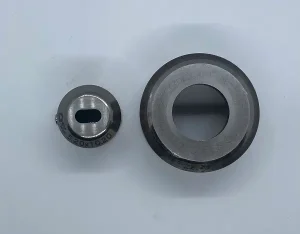
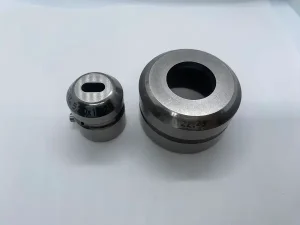
② クリアランス
下部金型(ダイ)の径 から 上部金型(パンチ)の径 を引いた隙間をクリアランスといいます。
上部金型(パンチ)よりも下部金型(ダイ)の径が少し大きくないと、材料を抜くことができないのです。
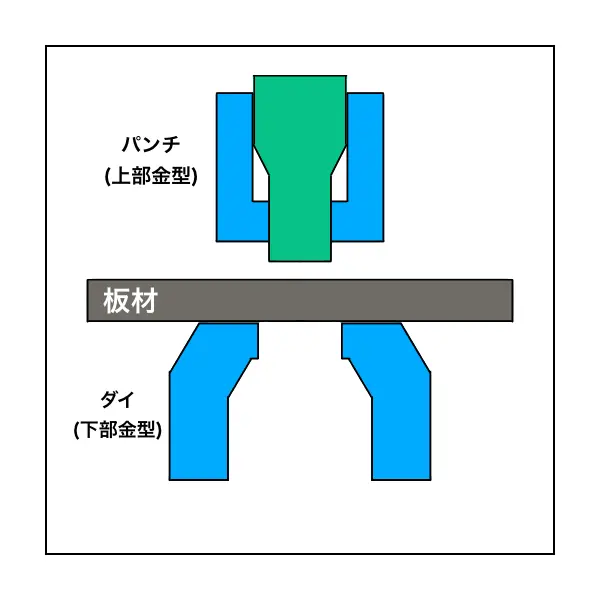
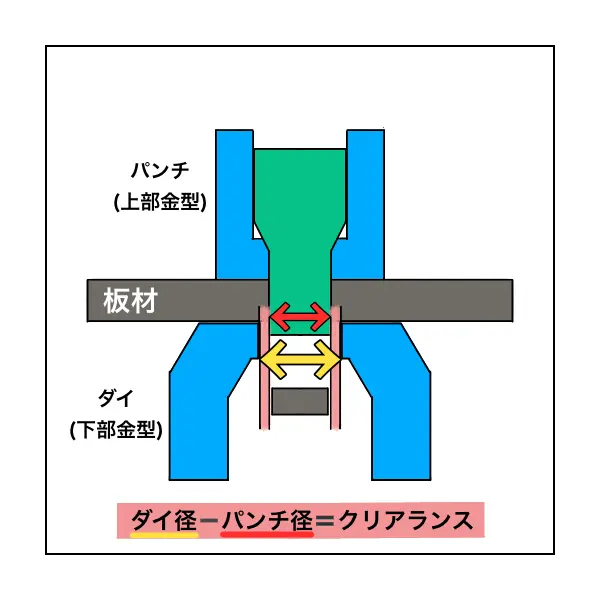
板厚や材質によって適正なクリアランスがあります。他にも用途や形状によってクリアランスの調整が必要です。
以下、株式会社アマダにより推奨されているクリアランス値です。
板厚(㎜) | 軟鋼 | アルミニウム | ステンレス |
---|---|---|---|
0.8 | 0.15~0.20 | 0.15~0.16 | 0.20~0.24 |
1.0 | 0.20~0.25 | 0.15~0.20 | 0.25~0.30 |
1.5 | 0.30~0.38 | 0.23~0.30 | 0.38~0.45 |
2.0 | 0.40~0.50 | 0.30~0.40 | 0.50~0.60 |
2.5 | 0.50~0.63 | 0.38~0.50 | 0.63~0.75 |
3.0 | 0.60~0.75 | 0.45~0.60 | 0.75~0.90 |
3.2 | 0.64~0.80 | 0.48~0.64 | 0.80~0.96 |
3.5 | 0.70~0.88 | 0.53~0.70 | 0.88~1.05 |
4.0 | 0.80~1.00 | 0.60~0.80 | 1.00~1.20 |
4.5 | 0.90~1.13 | 0.68~0.90 | 1.13~1.35 |
5.0 | 1.00~1.25 | 0.75~1.00 | ― |
5.5 | 1.10~1.38 | 0.83~1.10 | ― |
6.0 | 1.20~1.50 | 0.90~1.20 | ― |
出典:株式会社アマダ「NCT金型推奨クリアランス表」
https://navi.tooling.amada-vfactory.com/NAVI/Web_data/web_contents/Navi/PAGE_HTML/PT/Pt_Cl_help.html (最終アクセス2023年8月31日)
先程紹介した22Φの金型にも、ダイにはクリアランスが数種類あります。
「22.25Ф」と「22.5Ф」差は「0.25」ですが、材質や板厚によって適切なダイを選ぶ必要があります。
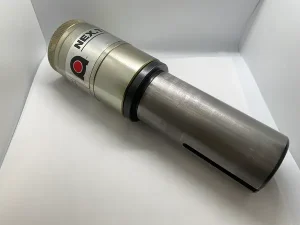
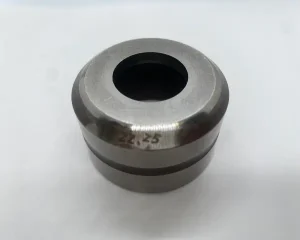
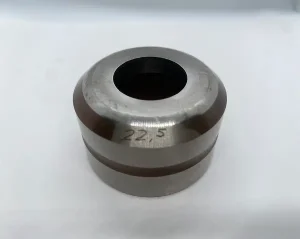
③ タレット
指定したタレット番号に金型をセットすることで、プログラムを読み込んで自動でタレットが回転し、
指定した金型を指定位置で打ち抜くことができます。約50種類もの金型をセットすることができるため、様々な形状の加工が可能です。
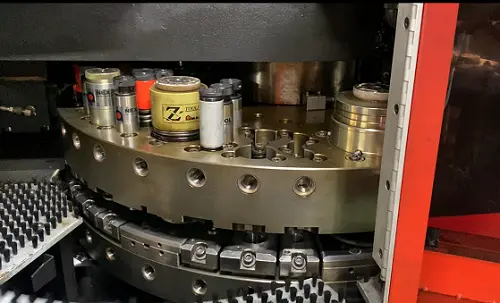
加工の種類
① 単発加工
丸・角・長丸・長角の汎用金型の形状のまま材料に抜き加工をすることです。
特に丸型は単発で加工する場合が多いため、所持する金型は100種類を超えるでしょう。
15Фや10Фなどの他、15.2Ф・15.5Ф・10.5Фなど “0.1㎜” 単位の金型があります。
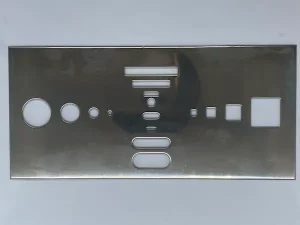
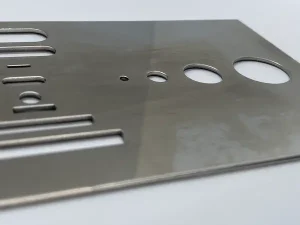
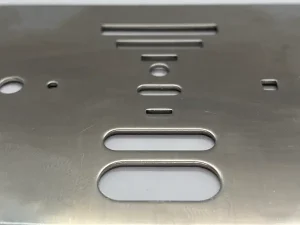
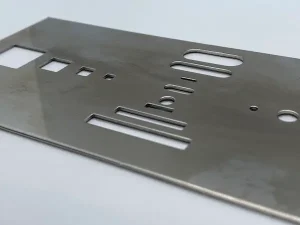
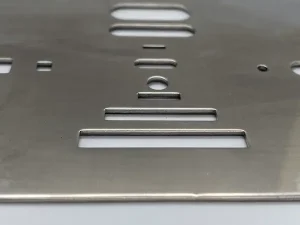
② 追い抜き加工
丸・角・長丸・長角だけでなく、複数の抜きを重ねることで様々な形状の加工も可能です。
また、外形加工は大半の場合、長角を使用した追い抜き加工を行います。
下図では、20×20の角型で追い抜き加工をしています。
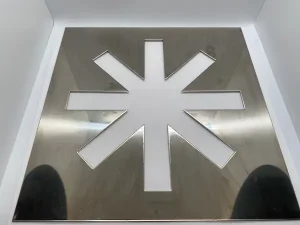
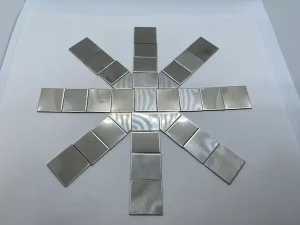
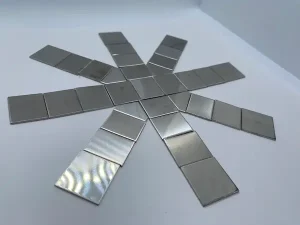
追い抜き加工の抜いた材料を見てみると、一つ一つ大きさや形状が異なっていることが分かります。
これは、金型への負担を軽減のため、加工する線長に合わせて金型が重なる部分の調整をしていることから
このような抜き方になります。
③ ニブリング加工
丸型で円やRの付いた形状を打ち抜く加工です。小さな丸型で多くの穴をあけることで材料を切断します。
そのため、切断面には細かい継ぎ目が発生します。実際現場では、円を抜くよりも角Rや曲線がある箇所にニブリング加工を使用することが多いです。
継ぎ目が出てしまうことや加工時間を考慮すると丸抜き加工や曲線などはレーザー加工を行うことが一般的です。
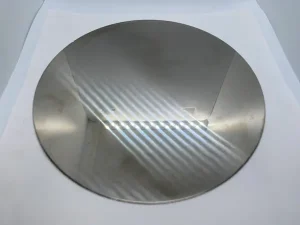
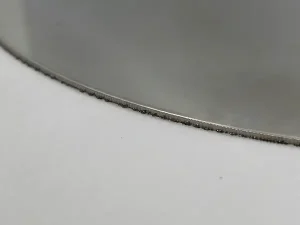
タレットパンチプレス加工のメリット
① 低コスト
レーザー加工と比較して
レーザー加工は、切断する際に特殊なガスを使用したり、消費電力が大きかったりとコストが高くなってしまいます。
プレス加工と比較して
プレス加工では、製品ごとの専用金型が必要となります。
製作数が「小ロット」「短期的な生産」の場合、金型作成は初期費用を多く占めてしまいます。
長期的に「生産個数が多い製品」の場合はプレス加工の方がコストが低くなる場合もあります。
② 穴あけ加工が速い
レーザー加工と比較すると、一回のパンチで穴あけ加工を行えるため、穴あけの加工速度が速いです。
連続で打ち抜くため、穴あけが多い形状ではタレットパンチプレスで加工する場合が多くなります。
タレットパンチプレスのデメリット
① 追い抜き跡
金型を組み合わせて材料を抜くため、切断面に継ぎ目の跡がどうしてもできてしまいます。シャーリングやレーザーの場合には継ぎ目は出ないため、製品によってはシャーリングやレーザーの加工を選択する必要があります。
② 形状の制限
丸・角・長丸・長角の組み合わせにより形状を加工するため、複雑な形状になると加工が困難になります。
その場合はレーザー加工もしくは、金型を発注することで対応する必要があります。
レーザー加工の様子を動画にしていますので、あわせてご覧ください。
まとめ
今回は、汎用金型の組み合わせよる、穴あけ加工や打ち抜き加工が可能な「タレットパンチプレス加工」について解説しました。小ロットから大量生産まで対応可能な、板金加工では中心となる機械です。
製品の特徴や形状によって、レーザー加工やプレス加工との選定が重要ですね。
当社では、タレットパンチプレス、レーザー加工機、プレス加工機等取り揃えております。お気軽にご相談ください。
この記事を書いた人
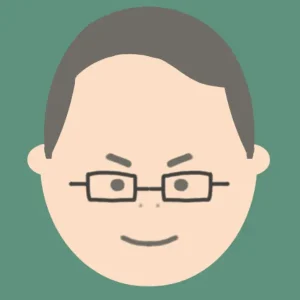
監修:社長
自営業で塗装業を経験後、金属加工業へ。
金属加工・精密板金の経験は30年以上。
現在社長9年目。社長就任後も現場で日々、模索し製作活動に励む。
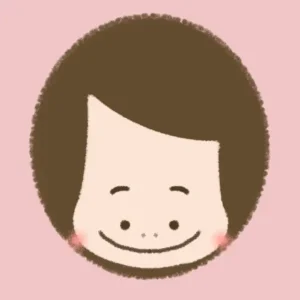
執筆:いくら
2023年6月からWordPress(ワードプレス)を始め、WEBやマーケティングについて勉強中。金属加工歴:3年
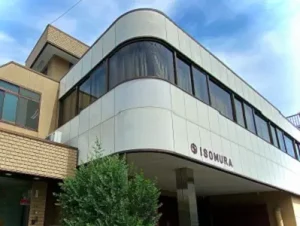
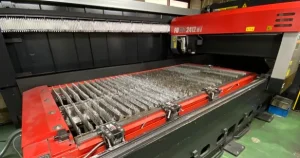
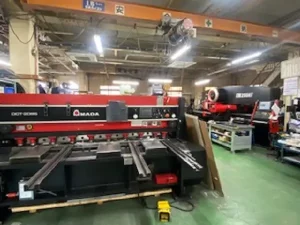